Case Study: How We Helped a Local Business Reduce Truck Downtime
Understanding the Challenge
When a local logistics company approached us with the challenge of reducing their truck downtime, we knew we had a significant task ahead. Downtime not only disrupts operations but also leads to increased costs and loss of revenue. The business was experiencing frequent truck breakdowns, which were affecting their delivery schedules and customer satisfaction.
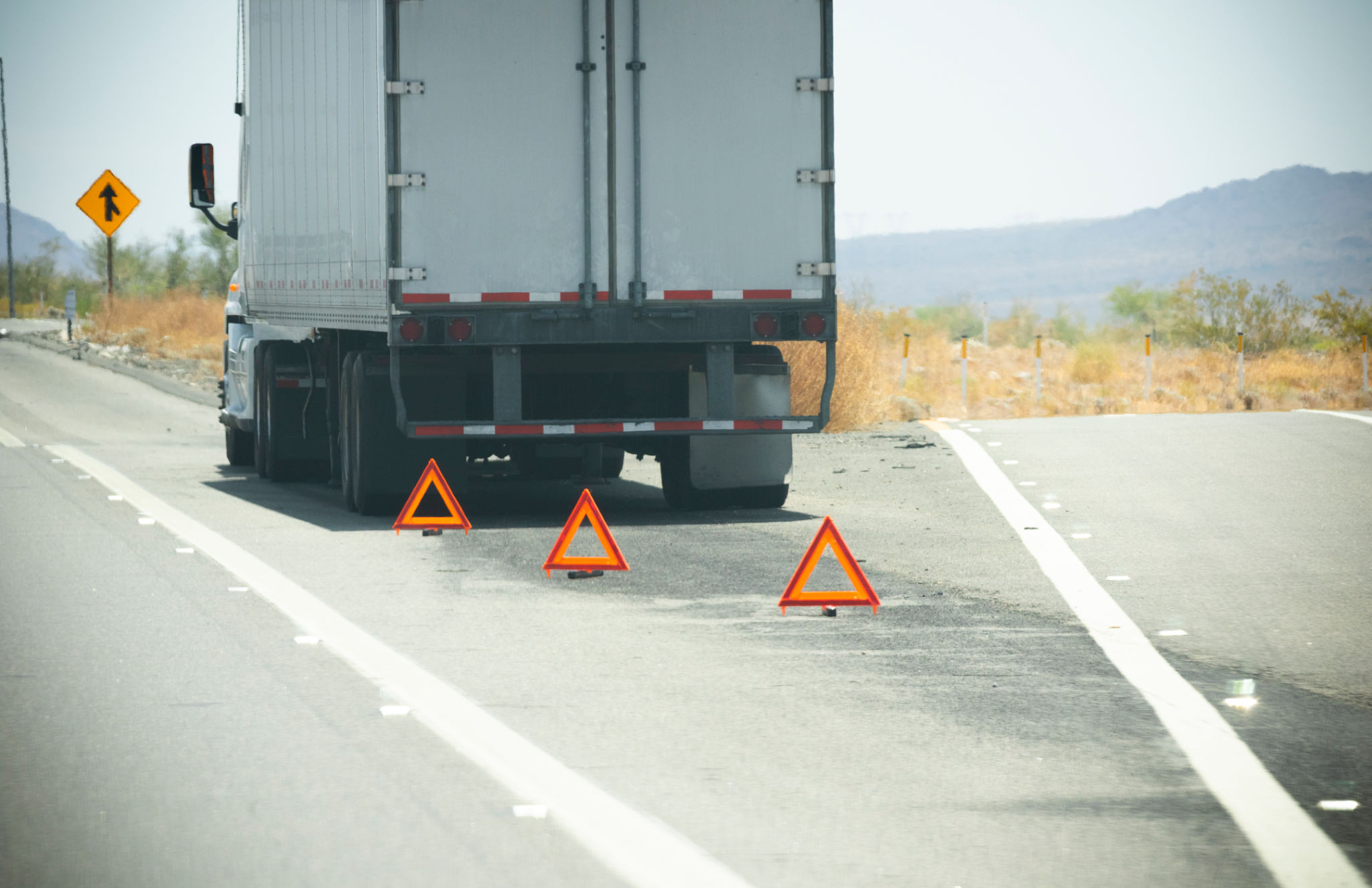
Our first step was to conduct a comprehensive analysis of the fleet's current maintenance schedule, repair history, and overall management practices. We discovered that the root causes of the downtime were irregular maintenance, lack of real-time monitoring, and inefficient repair processes.
Implementing a Preventive Maintenance Plan
Based on our findings, we proposed a robust preventive maintenance plan to keep the trucks in optimal condition. This plan included:
- Regularly scheduled inspections and servicing.
- Use of high-quality parts and fluids.
- Comprehensive training for the in-house maintenance team.
By implementing these measures, we aimed to identify potential issues before they escalated into costly repairs or breakdowns. The preventive maintenance plan significantly reduced unexpected failures and extended the lifespan of the fleet.
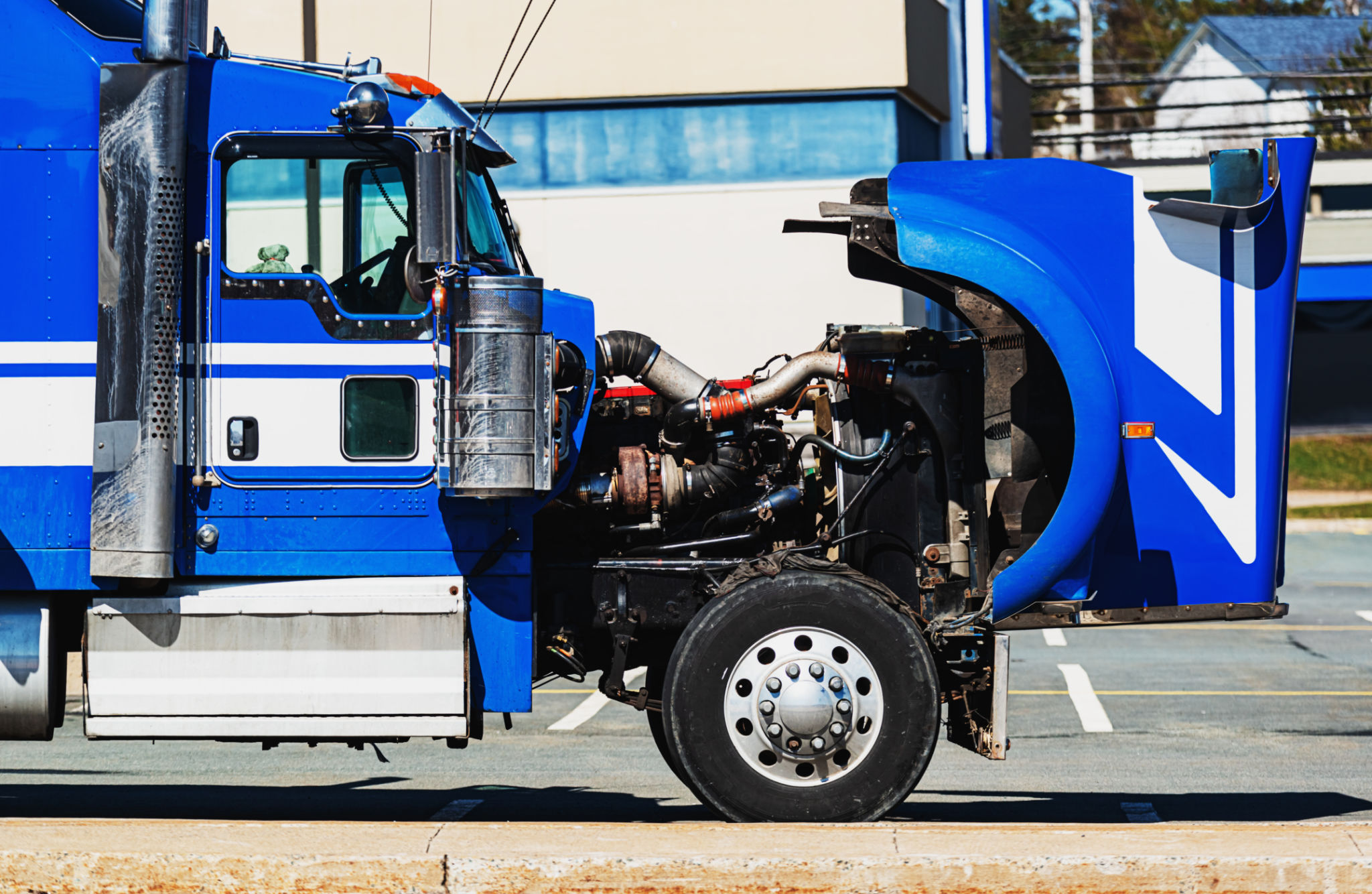
Leveraging Technology for Real-Time Monitoring
To further minimize downtime, we introduced an advanced fleet management system equipped with GPS tracking and telematics. This technology provided the company with real-time data on vehicle health, driver behavior, and route efficiency.
The system's predictive analytics capabilities alerted the team about potential issues before they occurred. This proactive approach allowed for timely interventions, reducing both repair times and overall downtime.
Streamlining Repair Processes
Another critical area was optimizing the repair processes. We collaborated with local repair shops to establish priority service agreements for quicker turnaround times. Additionally, we created a centralized inventory system for spare parts to ensure that necessary components were readily available when needed.
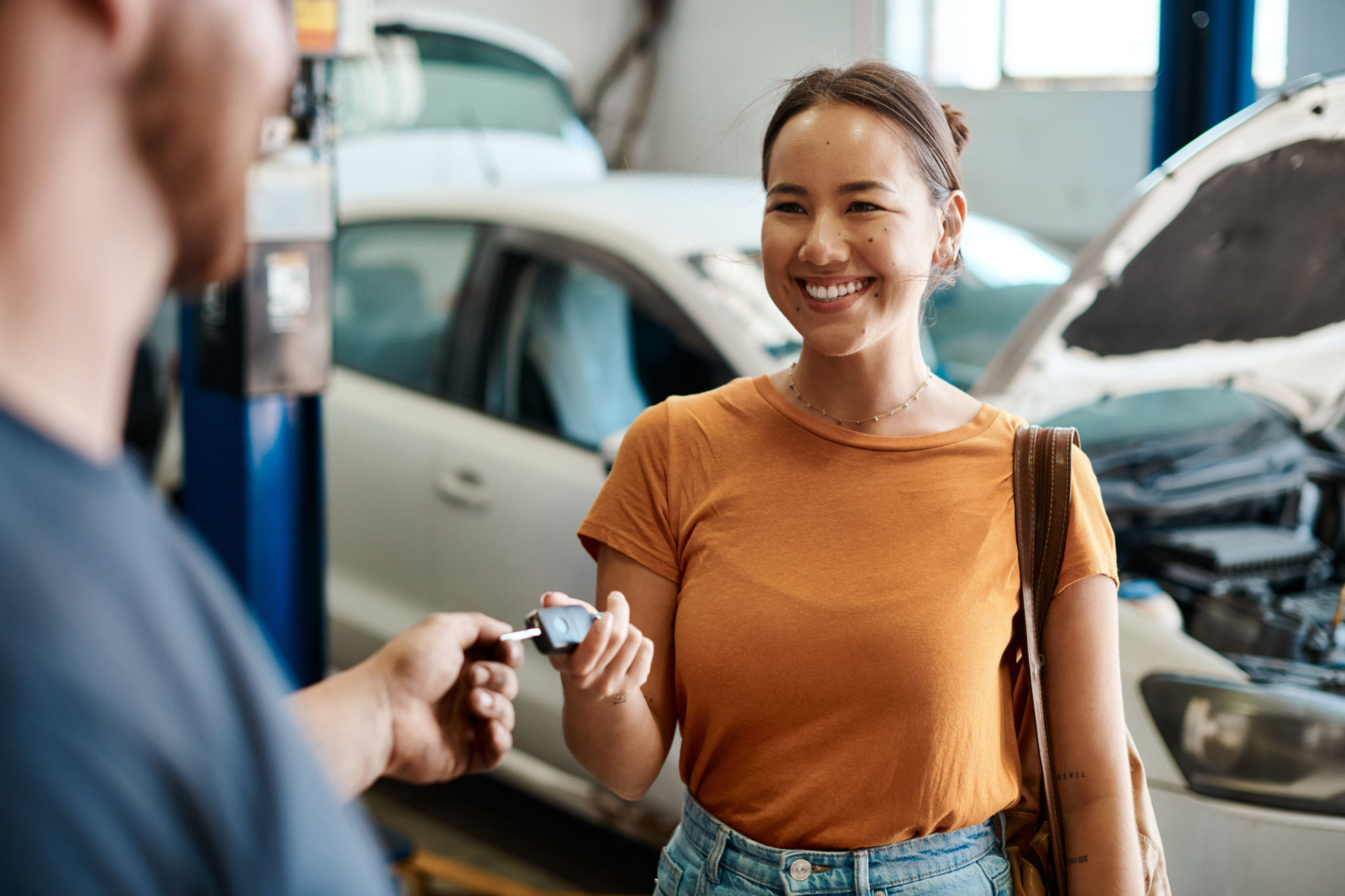
This streamlined approach cut down the waiting time for repairs and ensured that trucks returned to operation as swiftly as possible. The company's partnerships with reliable service providers also ensured consistent quality in maintenance work.
Achieving Results
Within six months of implementing these strategies, the logistics company witnessed a remarkable 40% reduction in truck downtime. This improvement not only enhanced their operational efficiency but also boosted their bottom line by reducing unnecessary expenses related to breakdowns and delays.
Customer satisfaction improved significantly as deliveries became more reliable and punctual. The company's reputation as a dependable logistics provider strengthened, leading to increased business opportunities and growth.
Conclusion
This case study demonstrates how a strategic approach to maintenance and technology integration can dramatically improve fleet efficiency. By focusing on proactive measures and efficient processes, businesses can minimize downtime and maximize productivity.
If your business is facing similar challenges, consider adopting a comprehensive strategy like this one to enhance your operational performance and drive success.